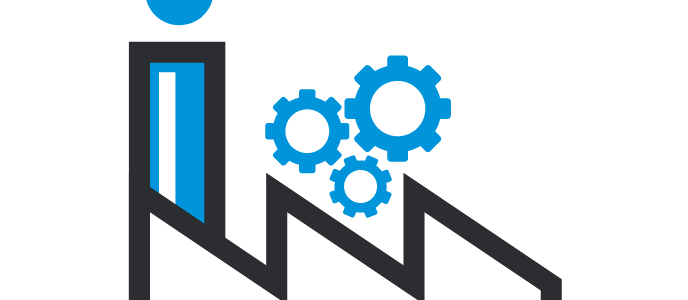
A Roadmap to Digital Transformation: Enhancing Productivity and Reducing Wastage in OEM Garment Manufacturing
In the fast-paced and competitive landscape of garment manufacturing, embracing digital transformation is crucial for traditional original equipment manufacturer (OEM) garment factories to remain agile, efficient, and sustainable. By leveraging digital technologies and data-driven insights, OEM garment factories can streamline production processes, optimize resource utilization, and minimize wastage, ultimately boosting productivity and enhancing competitiveness. In this comprehensive guide, we’ll outline a detailed roadmap for implementing digital transformation in an OEM garment factory to achieve these objectives, accompanied by relevant examples and best practices.
Important Notes: Even this article is sharing use-cases in Garment Factory, but it is still valuable for all manufacturing firms. |
1. Assessment and Strategy Development:
- The first step in embarking on a digital transformation journey is to conduct a comprehensive assessment of the factory’s current operations, capabilities, and pain points. This assessment should involve gathering input from key stakeholders across different departments to identify areas for improvement and prioritize strategic objectives. Based on the assessment findings, the factory can develop a clear digital transformation strategy aligned with its business goals and objectives.
- Example: a traditional OEM garment factory, conducts a thorough assessment of its production processes and identifies inefficiencies in material sourcing, production planning, and inventory management. Based on these findings, the factory develops a digital transformation strategy focused on implementing advanced planning and scheduling systems, adopting RFID technology for inventory tracking, and integrating data analytics for demand forecasting.
2. Investment in Digital Infrastructure:
- Building a robust digital infrastructure is essential for enabling the adoption of digital technologies and supporting data-driven decision-making. This may involve upgrading IT systems, investing in cloud computing platforms, and deploying sensors and IoT devices to collect real-time data from manufacturing equipment and processes. Additionally, the factory should prioritize cybersecurity measures to protect sensitive data and ensure operational continuity.
- Example: A Garment Firm invests in upgrading its legacy IT systems to a cloud-based ERP (Enterprise Resource Planning) solution that integrates seamlessly with its manufacturing equipment and enables real-time data exchange. Additionally, the firm deploys IoT sensors on its production lines to monitor machine performance and collect data on production output and quality metrics.
3. Implementation of Advanced Planning and Scheduling (APS) Systems:
- Advanced Planning and Scheduling (APS) systems use algorithms and optimization techniques to optimize production schedules, allocate resources efficiently, and minimize lead times. By implementing APS systems, OEM garment factories can improve production planning accuracy, reduce idle time, and enhance overall operational efficiency.
- Example: A Garment factory adopts an APS system that integrates with its ERP software to automate production scheduling and resource allocation based on demand forecasts, production capacity, and inventory levels. As a result, the factory achieves a significant reduction in lead times and inventory holding costs while improving on-time delivery performance.
4. Adoption of RFID Technology for Inventory Management:
- Radio Frequency Identification (RFID) technology enables real-time tracking and monitoring of inventory throughout the supply chain, from raw materials to finished products. By implementing RFID systems, OEM garment factories can improve inventory visibility, reduce stockouts and overstocking, and enhance order fulfillment efficiency.
- Example: A large scale Garment manufacturing company deploys RFID tags on its raw materials, work-in-progress (WIP) inventory, and finished goods, allowing for seamless tracking and monitoring throughout the production process. The company integrates RFID data with its ERP system to optimize inventory levels, identify bottlenecks, and improve production planning accuracy.
5. Integration of Data Analytics for Demand Forecasting:
- Data analytics tools and techniques can provide valuable insights into customer preferences, market trends, and demand patterns. By analyzing historical sales data, market trends, and customer feedback, OEM garment factories can develop more accurate demand forecasts, optimize production planning, and reduce the risk of overproduction or stockouts.
- Example: A garment factory leverages data analytics to analyze historical sales data, social media trends, and customer feedback to identify emerging fashion trends and forecast demand for its products. The factory uses predictive analytics models to generate demand forecasts for different product categories and sizes, enabling more accurate production planning and inventory management.
6. Implementation of Lean Manufacturing Principles:
- Lean manufacturing principles, such as Just-in-Time (JIT) production, Kanban systems, and continuous improvement initiatives, are essential for reducing waste, improving efficiency, and optimizing resource utilization in garment manufacturing. By embracing lean principles, OEM garment factories can minimize lead times, reduce excess inventory, and enhance overall operational agility.
- Example: A large garment manufacturing firm adopts lean manufacturing principles and implements Kanban systems to optimize material flow and production processes. The company establishes visual management systems on the factory floor to monitor production progress, identify bottlenecks, and empower employees to identify and address inefficiencies in real time.
7. Employee Training and Change Management:
- Digital transformation requires a cultural shift and ongoing employee training to ensure successful adoption and implementation of new technologies and processes. OEM garment factories should invest in comprehensive training programs to upskill employees, foster a culture of innovation, and promote continuous learning and improvement.
- Example: A garment factory provides extensive training to its workforce on the use of new digital tools and technologies, such as ERP systems, APS software, and RFID technology. The factory also establishes cross-functional teams to drive digital transformation initiatives and encourages employee participation in process improvement projects.
8. Continuous Monitoring and Improvement:
- Digital transformation is an ongoing process that requires continuous monitoring, evaluation, and adaptation to changing market dynamics and technological advancements. OEM garment factories should establish key performance indicators (KPIs) to track progress, identify areas for improvement, and iterate on digital transformation initiatives to drive sustainable growth and competitiveness.
- Example: A Hong Kong based Garment company establishes a digital transformation steering committee tasked with monitoring KPIs, conducting regular performance reviews, and identifying opportunities for process optimization and innovation. The company also solicits feedback from employees and stakeholders to identify pain points and areas for improvement, fostering a culture of continuous improvement and innovation.
Remark: all garment factory use-cases needed to be anonymous due to NDA agreement.
In conclusion, implementing digital transformation initiatives is essential for OEM garment factories to enhance productivity, reduce wastage, and remain competitive in today’s rapidly evolving market. By adopting a strategic approach to digital transformation, leveraging advanced technologies, and embracing a culture of innovation and continuous improvement, OEM garment factories can streamline production processes, optimize resource utilization, and drive sustainable growth and profitability. By following the detailed roadmap outlined in this guide and learning from relevant examples and best practices, OEM garment factories can navigate the complexities of digital transformation successfully and realize the full potential of digital technologies to transform their operations and achieve business objectives.